کراکینگ بخار یک فرآیند پتروشیمی در مینی پالایشگاه و پالایشگاه ها است که در آن هیدروکربن های اشباع شده به هیدروکربن های کوچکتر و اغلب غیراشباع تجزیه می شوند. این روش صنعتی اصلی برای تولید آلکنهای سبکتر (یا معمولاً الفینها)، از جمله اتن (یا اتیلن) و پروپن (یا پروپیلن) است.
واحدهای کراکر بخار تأسیساتی هستند که در آن مواد اولیه مانند نفتا، گاز مایع (LPG)، اتان، پروپان یا بوتان از طریق استفاده از بخار در کوره های کراکینگ بخار برای تولید هیدروکربن های سبک تر، ترک خورده می شوند.
فرآیند هیدروژن زدایی پروپان ممکن است از طریق فناوری های تجاری مختلف انجام شود. تفاوت اصلی بین هر یک از آنها مربوط به کاتالیزور مورد استفاده، طراحی راکتور و استراتژی برای دستیابی به نرخ تبدیل بالاتر است.
الفین ها پیش سازهای مفیدی برای محصولات بی شمار هستند. کراکینگ با بخار فناوری اصلی است که از بزرگترین مقیاس فرآیندهای شیمیایی پشتیبانی می کند. اتیلن و پروپیلن
شرح فرایند کراکینگ بخار
در کراکینگ بخار، یک خوراک هیدروکربنی گازی یا مایع مانند نفتا، LPG یا اتان با بخار رقیق میشود و در غیاب اکسیژن برای مدت کوتاهی در کوره گرم میشود.به طور معمول، دمای واکنش بسیار بالا و در حدود 850 درجه سانتیگراد است.
واکنش به سرعت رخ می دهد: زمان ماندن در حدود میلی ثانیه است. نرخ جریان به سرعت صوت نزدیک می شود. پس از رسیدن به دمای ترک، گاز به سرعت خاموش می شود تا واکنش در یک مبدل حرارتی خط انتقال یا داخل یک هدر خاموش کننده با استفاده از روغن کوئنچ متوقف شود.
محصولات تولید شده در واکنش به ترکیب خوراک، نسبت هیدروکربن به بخار و دمای ترک و زمان ماندن کوره بستگی دارد. خوراکهای هیدروکربنی سبک مانند اتان، LPG یا نفتای سبک عمدتاً آلکنهای سبکتری از جمله اتیلن، پروپیلن و بوتادین میدهند.
هیدروکربنهای سنگینتر (فول برد و نفتاهای سنگین و همچنین سایر محصولات پالایشگاهی) برخی از همین محصولات را تولید میکنند، اما همچنین آنهایی که غنی از هیدروکربنهای معطر و هیدروکربنهای مناسب برای گنجاندن در بنزین یا نفت کوره هستند.
دمای ترک بالاتر (که به آن شدت نیز گفته می شود) به تولید اتن و بنزن کمک می کند، در حالی که شدت کمتر باعث تولید مقادیر بالاتر پروپن، هیدروکربن های C4 و محصولات مایع می شود. این فرآیند همچنین منجر به رسوب آهسته کک، شکلی از کربن، بر روی دیواره های راکتور می شود.
این کارایی راکتور را کاهش می دهد، بنابراین شرایط واکنش طوری طراحی شده است که این را به حداقل برساند. با این وجود، یک کوره کراکینگ بخار معمولاً تنها می تواند چند ماه در فاصله زمانی بین کک زدایی کار کند.
دکوک ها نیاز دارند که کوره از فرآیند جدا شود و سپس جریانی از بخار یا مخلوط بخار/هوا از سیم پیچ های کوره عبور داده شود. این لایه کربن جامد سخت را به مونوکسید کربن و دی اکسید کربن تبدیل می کند. هنگامی که این واکنش کامل شد، کوره را می توان به خدمت بازگرداند.
جزئیات فرآیند کراکینگ بخار
مناطق یک کارخانه اتیلن عبارتند از:
- کوره های کراکینگ بخار
- بازیابی حرارت اولیه و ثانویه با کوئنچ.
- یک سیستم بازیافت بخار رقیق بین کوره ها و سیستم کوئنچ.
- فشرده سازی اولیه گاز ترک خورده (3 مرحله فشرده سازی).
- حذف سولفید هیدروژن و دی اکسید کربن (حذف گاز اسیدی)؛
- فشرده سازی ثانویه (1 یا 2 مرحله)؛
- خشک کردن گاز ترک خورده؛
- درمان برودتی؛
- تمام جریان گاز سرد ترک خورده به برج دی متانیزر می رود. جریان بالای برج گاز زدایی از تمام هیدروژن و متان موجود در جریان گاز ترک خورده تشکیل شده است. به طور برودتی (-250 درجه فارنهایت (-157 درجه سانتیگراد)) با تصفیه این جریان بالای سر، هیدروژن را از متان جدا می کند. بازیافت متان برای عملکرد اقتصادی یک کارخانه اتیلن حیاتی است.
- جریان پایینی از برج فلز زدایی به سمت برج فلز زدایی می رود. جریان بالای برج دمپاشکننده شامل تمام C2هایی است که در جریان گاز ترک خورده بودند. جریان C2 حاوی استیلن است که بیش از 200 کیلو پاسکال (29 psi) قابل انفجار است. اگر انتظار می رود فشار جزئی استیلن از این مقادیر بیشتر شود، جریان C2 تا حدی هیدروژنه می شود. سپس C2 به یک تقسیم کننده C2 ادامه می دهد. اتیلن محصول از بالای برج گرفته می شود و اتانی که از پایین شکاف می آید به کوره ها بازیافت می شود تا دوباره ترک شود.
- جریان پایینی از برج اتانایزر به سمت برج depropanizer می رود. جریان بالای سر از برج depropanizer شامل تمام C3هایی است که در جریان گاز ترک خورده بودند. قبل از تغذیه C3 به شکاف کننده C3، جریان هیدروژنه می شود تا مخلوط متیل استیلن و پروپادین (آلن) تبدیل شود. سپس این جریان به اسپلیتر C3 ارسال می شود. جریان سربار اسپلیتر C3 پروپیلن محصول و جریان پایین پروپان است که برای ترک خوردن به کوره ها فرستاده می شود یا به عنوان سوخت استفاده می شود.
- جریان پایین از برج depropanizer به برج debutanizer تغذیه می شود. جریان بالای سر از دیبوتانایزر تمام C4هایی است که در جریان گاز ترک خورده قرار داشتند. جریان پایین از دیبوتانایزر (بنزین پیرولیز سبک) از هر چیزی در جریان گاز ترک خورده تشکیل شده است که C5 یا سنگین تر است.
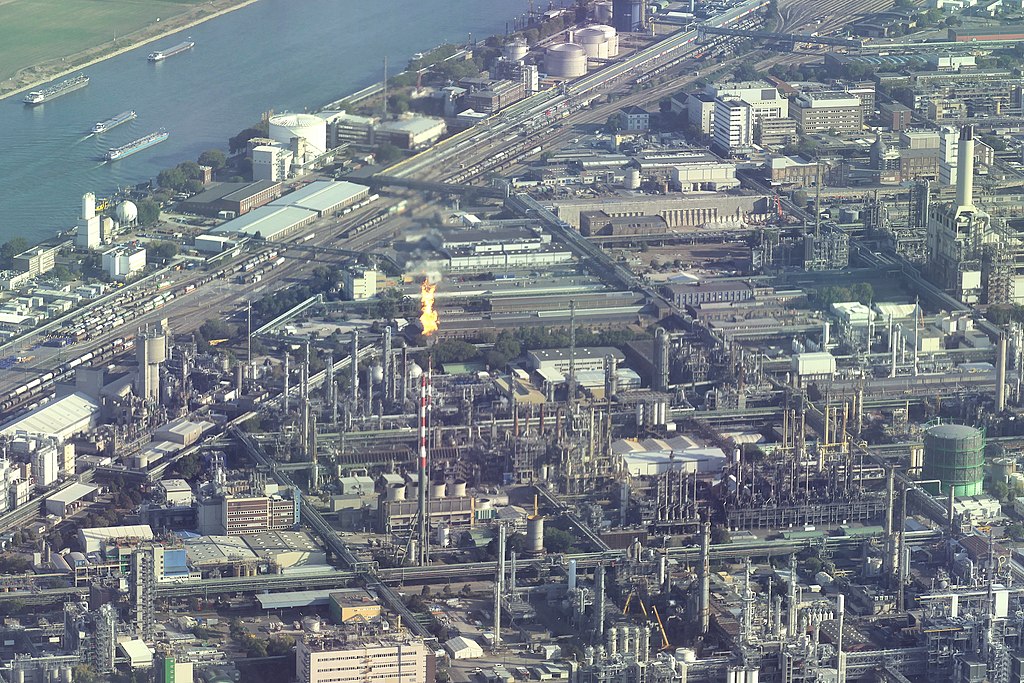
از آنجایی که تولید اتیلن انرژی بر است، تلاش زیادی برای بازیابی گرما از گاز خروجی از کوره ها انجام شده است. بیشتر انرژی بازیافت شده از گاز ترک خورده برای تولید بخار با فشار بالا (1200 psig (8300 کیلو پاسکال)) استفاده می شود.
این بخار به نوبه خود برای به حرکت درآوردن توربین ها برای فشرده سازی گاز ترک خورده، کمپرسور تبرید پروپیلن و کمپرسور تبرید اتیلن استفاده می شود. یک کارخانه اتیلن پس از راه اندازی، نیازی به واردات بخار برای به حرکت درآوردن توربین های بخار خود ندارد. یک کارخانه معمولی اتیلن در مقیاس جهانی (حدود 1.5 میلیارد پوند (680 KTA) اتیلن در سال) از یک کمپرسور گاز ترک خورده با قدرت 45000 اسب بخار (34000 کیلووات)، یک کمپرسور پروپیلن 30000 اسب بخار (22000 کیلووات) و یک کمپرسور پروپیلن با قدرت 30000 اسب بخار استفاده می کند.
حتی با وجود ادغام کامل انرژی در یک کارخانه کراکینگ بخار، این فرآیند مقدار غیر قابل حلی از دی اکسید کربن تولید می کند. در هر تن اتیلن، 1 تا 1.6 تن دی اکسید کربن (بسته به ماده اولیه) تولید می شود.
در نتیجه مقدار سرسام آور بیش از 300 میلیون تن دی اکسید کربن سالانه در جو منتشر می شود که 70 تا 90 درصد آن مستقیماً به احتراق سوخت فسیلی نسبت داده می شود. در چند دهه اخیر، پیشرفتهای متعددی در فناوری کراکینگ با بخار برای افزایش بهرهوری انرژی انجام شده است.
این تغییرات شامل احتراق سوخت اکسی، فناوری مشعل جدید، و هندسه رآکتور سه بعدی است. با این حال، همانطور که در فنآوریهای بالغ معمول است، این تغییرات تنها به دستاوردهای نهایی در بهرهوری انرژی منجر شد.
برای مهار شدید انتشار گازهای گلخانهای ناشی از ترکخوردگی بخار، برقرسانی راهحلی را ارائه میدهد زیرا برق تجدیدپذیر میتواند مستقیماً با گرمایش مقاومتی و القایی به طور مستقیم به گرما تبدیل شود.
در نتیجه، چندین شرکت پتروشیمی به نیروها پیوستند که منجر به توسعه چندین توافقنامه مشترک شد که در آنها تلاشهای تحقیق و توسعه را برای بررسی چگونگی استفاده از کراکرهای نفتا یا بخار گازی با استفاده از برق تجدیدپذیر به جای احتراق سوخت فسیلی ترکیب کردند.
بدون دیدگاه