کراکینگ، در پالایش نفت، فرآیندی است که در پالایشگاه ها و مینی پالایشگاه طی آن مولکولهای هیدروکربن سنگین توسط گرما و معمولاً فشار و گاهی اوقات کاتالیزورها به مولکولهای سبکتر تجزیه میشوند. کراکینگ مهمترین فرآیند برای تولید تجاری بنزین و سوخت دیزل است.
شکستن نفت باعث تولید روغنهای سبک (مرتبط با بنزین)، روغنهای رده متوسط مورد استفاده در سوخت دیزل، روغنهای سنگین باقیمانده، یک محصول کربنی جامد به نام کک و گازهایی مانند متان، اتان، اتیلن، پروپان، پروپیلن و بوتیلن میشود.
بسته به محصول نهایی، روغنها میتوانند مستقیماً وارد ترکیب سوخت شوند، یا میتوانند از طریق واکنشهای ترکخوردگی بیشتر یا سایر فرآیندهای پالایشی تا زمانی که روغنهایی با وزن مورد نظر تولید کنند، هدایت شوند.
این گازها را می توان در سیستم سوخت پالایشگاه استفاده کرد، اما آنها همچنین مواد خام مهمی برای کارخانه های پتروشیمی هستند، جایی که آنها را به تعداد زیادی محصول نهایی، از لاستیک مصنوعی و پلاستیک گرفته تا مواد شیمیایی کشاورزی، تبدیل می کنند.
تاریخچه کراکینگ
اولین فرآیند ترک حرارتی برای تجزیه هیدروکربن های بزرگ غیرفرار به بنزین در سال 1913 مورد استفاده قرار گرفت. توسط ویلیام مریام برتون، شیمیدانی که برای شرکت استاندارد اویل (ایندیانا) کار می کرد، اختراع شد که بعداً به شرکت آموکو تبدیل شد.
در دهه 1920 پیشرفت های مختلفی برای ترک حرارتی ارائه شد. همچنین در دهه 1920، شیمیدان فرانسوی Eugène Houdry فرآیند کراکینگ را با کاتالیزورها بهبود بخشید تا محصولی با اکتان بالاتر به دست آورد.
فرآیند او در سال 1936 توسط شرکت نفتی Socony-Vacuum (بعدها شرکت Mobil Oil) و در سال 1937 توسط شرکت Sun Oil (بعدها Sunoco، Inc.) معرفی شد. ترک کاتالیستی خود در دهه 1940 با استفاده از بسترهای سیال یا متحرک کاتالیزور پودری بهبود یافت.
در طول دهه 1950، با افزایش تقاضا برای سوخت خودرو و جت، هیدروکراکینگ برای پالایش نفت اعمال شد. این فرآیند از گاز هیدروژن برای بهبود نسبت هیدروژن به کربن در مولکول های ترک خورده و رسیدن به طیف وسیع تری از محصولات نهایی مانند بنزین، نفت سفید (مورد استفاده در سوخت جت) و سوخت دیزل استفاده می کند. هیدروکراکینگ مدرن در دمای پایین در سال 1963 توسط شرکت استاندارد اویل کالیفرنیا (بعدها شرکت شورون) به تولید تجاری رسید.
متدولوژی های کراکینگ
کراکینگ حرارتی
کراکینگ حرارتی فشار بالا مدرن در فشار مطلق حدود 7000 کیلو پاسکال عمل می کند. یک فرآیند کلی از عدم تناسب را می توان مشاهده کرد، که در آن محصولات “سبک” غنی از هیدروژن به هزینه مولکول های سنگین تر که متراکم می شوند و از هیدروژن تهی می شوند، تشکیل می شوند. واکنش واقعی به عنوان شکافت همولیتیک شناخته می شود و آلکن ها را تولید می کند که اساس تولید پلیمرها از نظر اقتصادی مهم هستند.
کراکینگ حرارتی در حال حاضر برای “به روز رسانی” فراکسیون های بسیار سنگین یا تولید فراکسیون های سبک یا تقطیرها، سوخت مشعل و/یا کک نفتی استفاده می شود.
دو حالت افراطی از ترکخوردگی حرارتی بر حسب محدوده محصول توسط فرآیند با دمای بالا به نام “ترک بخار با بخار” یا پیرولیز (حدود 750 درجه سانتیگراد تا 900 درجه سانتیگراد یا بالاتر) نشان داده میشود که اتیلن با ارزش و سایر مواد اولیه را برای پتروشیمی تولید میکند. صنعت، و ککسازی تاخیری در دمای ملایمتر (حدود 500 درجه سانتیگراد) که میتواند در شرایط مناسب، کک سوزنی ارزشمند، یک کک نفتی بسیار کریستالی که در تولید الکترود برای صنایع فولاد و آلومینیوم استفاده میشود، تولید کند. ]
ویلیام مریام برتون یکی از اولین فرآیندهای ترک حرارتی را در سال 1912 توسعه داد که در دمای 700-750 درجه فارنهایت (370-400 درجه سانتیگراد) و فشار مطلق 90 psi (620 کیلو پاسکال) کار می کرد و به عنوان فرآیند برتون شناخته می شد.
اندکی پس از آن، در سال 1921، C.P. دابز، کارمند شرکت فراوردههای نفتی جهانی، فرآیند ترکخوردگی حرارتی تا حدودی پیشرفتهتری را ایجاد کرد که در دمای 750 تا 860 درجه فارنهایت (400 تا 460 درجه سانتیگراد) کار میکرد و به فرآیند دوبس معروف بود. تا اوایل دهه 1940 که کراکینگ کاتالیزوری مورد استفاده قرار گرفت، فرآیند دابس به طور گسترده توسط بسیاری از پالایشگاه ها مورد استفاده قرار گرفت.
کراکینگ بخار
کراکینگ با بخار یک فرآیند پتروشیمی است که در آن هیدروکربن های اشباع شده به هیدروکربن های کوچکتر و اغلب غیراشباع تجزیه می شوند. این روش صنعتی اصلی برای تولید آلکنهای سبکتر (یا معمولاً الفینها)، از جمله اتن (یا اتیلن) و پروپن (یا پروپیلن) است. واحدهای کراکر بخار تأسیساتی هستند که در آنها مواد اولیه مانند نفتا، گاز مایع (LPG)، اتان، پروپان یا بوتان از طریق استفاده از بخار در یک بانک کوره های پیرولیز برای تولید هیدروکربن های سبک تر، ترک خورده می شوند.
در کراکینگ بخار، یک خوراک هیدروکربنی گازی یا مایع مانند نفتا، LPG یا اتان با بخار رقیق شده و برای مدت کوتاهی در کوره بدون حضور اکسیژن گرم می شود. به طور معمول، دمای واکنش بسیار بالا است، در حدود 850 درجه سانتیگراد، اما واکنش فقط برای مدت کوتاهی مجاز است.
در کوره های کراکینگ مدرن، زمان ماندن به میلی ثانیه کاهش می یابد تا بازدهی بهبود یابد و در نتیجه سرعت گاز تا سرعت صوت افزایش می یابد. پس از رسیدن به دمای ترک، گاز به سرعت خاموش می شود تا واکنش در یک مبدل حرارتی خط انتقال یا داخل یک هدر خاموش کننده با استفاده از روغن کوئنچ متوقف شود.
محصولات تولید شده در واکنش به ترکیب خوراک، نسبت هیدروکربن به بخار و دمای ترک و زمان ماندن کوره بستگی دارد.
خوراکهای هیدروکربنی سبک مانند اتان، LPG یا نفتای سبک، جریانهای محصولی غنی از آلکنهای سبکتر از جمله اتیلن، پروپیلن و بوتادین میدهند. هیدروکربنهای سنگینتر (نفتاهای سنگین و کامل و همچنین سایر محصولات پالایشگاهی) برخی از این موارد را فراهم میکنند، اما همچنین محصولاتی غنی از هیدروکربنهای معطر و هیدروکربنهای مناسب برای گنجاندن در بنزین یا نفت کوره به دست میدهند. جریان های محصول معمولی شامل بنزین پیرولیز (pygas) و BTX است.
دمای ترک بالاتر (که به آن شدت نیز گفته می شود) به نفع تولید اتیلن و بنزن است، در حالی که شدت کمتر باعث تولید مقادیر بیشتری از پروپیلن، هیدروکربن های C4 و محصولات مایع می شود. این فرآیند همچنین منجر به رسوب آهسته کک، شکلی از کربن، بر روی دیواره های راکتور می شود.
از آنجایی که کک کارایی راکتور را کاهش می دهد، دقت زیادی برای طراحی شرایط واکنش برای به حداقل رساندن تشکیل آن انجام می شود. با این وجود، یک کوره کراکینگ بخار معمولاً فقط می تواند چند ماه بین کک زدایی کار کند. “دکک ها” نیاز دارند که کوره از فرآیند جدا شود و سپس جریانی از بخار یا مخلوط بخار/هوا از سیم پیچ های کوره عبور داده شود. این دک کردن اساساً احتراق کربن است و لایه کربن جامد سخت را به مونوکسید کربن و دی اکسید کربن تبدیل می کند.
کراکینگ کاتالیزوری سیال
فرآیند کراکینگ کاتالیزوری شامل حضور کاتالیزورهای اسید جامد، معمولاً سیلیس- آلومینا و زئولیت است. کاتالیزورها باعث تشکیل کربوکاتیونها میشوند که تحت فرآیندهای بازآرایی و بریدگی پیوندهای C-C قرار میگیرند. نسبت به ترک حرارتی، ترک خوردن گربه در دماهای ملایم تر انجام می شود که باعث صرفه جویی در انرژی می شود. علاوه بر این، با عملکرد در دماهای پایین تر، بازده آلکن ها کاهش می یابد. آلکن ها باعث ناپایداری سوخت های هیدروکربنی می شوند.
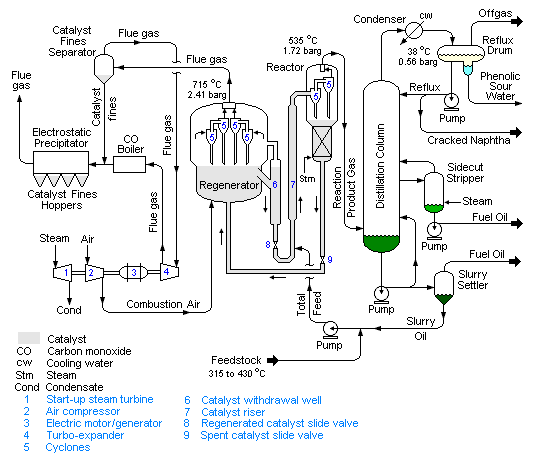
کراکینگ کاتالیزوری سیال فرآیندی است که معمولاً مورد استفاده قرار می گیرد، و یک پالایشگاه نفت مدرن معمولاً شامل یک کراکر گربه ای است، به ویژه در پالایشگاه های ایالات متحده، به دلیل تقاضای زیاد برای بنزین.
این فرآیند برای اولین بار در حدود سال 1942 مورد استفاده قرار گرفت و از یک کاتالیزور پودری استفاده کرد. در طول جنگ جهانی دوم، نیروهای متفقین منابع فراوانی از مواد داشتند، برخلاف نیروهای محور که با کمبود شدید بنزین و لاستیک مصنوعی مواجه بودند. اجرای فرآیند اولیه بر اساس کاتالیزور آلومینا با فعالیت کم و راکتوری بود که در آن ذرات کاتالیزور در یک جریان فزاینده هیدروکربن های خوراک در یک بستر سیال معلق بودند.
در طرحهای جدیدتر، ترکخوردگی با استفاده از یک کاتالیزور بسیار فعال مبتنی بر زئولیت در یک لوله عمودی یا با شیب رو به بالا با زمان تماس کوتاه به نام «رایزر» صورت میگیرد. خوراک از پیش گرم شده از طریق نازل های تغذیه به پایه رایزر اسپری می شود که در آنجا با کاتالیزور سیال بسیار داغ در دمای 1230 تا 1400 درجه فارنهایت (666 تا 760 درجه سانتی گراد) تماس می گیرد.
کاتالیزور داغ خوراک را تبخیر می کند و واکنش های ترک خوردگی را کاتالیز می کند که روغن با وزن مولکولی بالا را به اجزای سبک تر از جمله LPG، بنزین و گازوئیل تجزیه می کند. مخلوط کاتالیزور-هیدروکربن برای چند ثانیه از طریق رایزر به سمت بالا جریان می یابد و سپس مخلوط از طریق سیکلون ها جدا می شود.
هیدروکربنهای بدون کاتالیزور برای جداسازی به گازهای سوختی، LPG، بنزین، نفتا، روغنهای چرخه سبک مورد استفاده در دیزل و سوخت جت، و نفت کوره سنگین به یک قطعهساز اصلی هدایت میشوند.
در طول سفر به بالابر، کاتالیزور کراکینگ توسط واکنشهایی که کک را روی کاتالیست رسوب میکند و فعالیت و گزینشپذیری را تا حد زیادی کاهش میدهد، «هزینه» میشود.
کاتالیزور مصرف شده از بخارات هیدروکربن ترک خورده جدا می شود و به یک دستگاه استریپر فرستاده می شود که در آنجا با بخار تماس می گیرد تا هیدروکربن های باقی مانده در منافذ کاتالیزور را حذف کند.
سپس کاتالیزور «صرفشده» به یک بازسازیکننده بستر سیال جریان مییابد که در آن از هوا (یا در برخی موارد هوا به اضافه اکسیژن) برای سوزاندن کک برای بازگرداندن فعالیت کاتالیزور و همچنین تأمین گرمای لازم برای چرخه واکنش بعدی استفاده میشود. واکنش گرماگیر سپس کاتالیزور “بازسازی شده” به سمت پایه رایزر جریان می یابد و چرخه را تکرار می کند.
بنزین تولید شده در واحد FCC دارای رتبه اکتان بالا است اما به دلیل مشخصات الفینیک آن در مقایسه با سایر اجزای بنزین از پایداری شیمیایی کمتری برخوردار است. الفین های موجود در بنزین مسئول تشکیل رسوبات پلیمری در مخازن ذخیره، مجاری سوخت و انژکتورها هستند. FCC LPG منبع مهمی از الفین های C3-C4 و ایزوبوتان است که خوراک ضروری برای فرآیند آلکیلاسیون و تولید پلیمرهایی مانند پلی پروپیلن هستند.
هیدروکراکینگ
هیدروکراکینگ یک فرآیند کراکینگ کاتالیستی است که با حضور گاز هیدروژن اضافه شده کمک می کند. بر خلاف هیدروکراکینگ، هیدروکراک از هیدروژن برای شکستن پیوندهای C-C استفاده می کند (هیدروکراک قبل از هیدروکراکینگ برای محافظت از کاتالیزورها در فرآیند هیدروکراکینگ انجام می شود).
در سال 2010، 265 × 106 تن نفت با این فناوری فرآوری شد. خوراک اصلی نفت گاز خلاء است که بخش سنگینی از نفت است.
محصولات این فرآیند هیدروکربن های اشباع هستند. بسته به شرایط واکنش (دما، فشار، فعالیت کاتالیزور) این محصولات از اتان، LPG تا هیدروکربنهای سنگینتر که عمدتاً از ایزوپارافین تشکیل شدهاند، متغیر است.
هیدروکراکینگ معمولاً توسط یک کاتالیزور دو عملکردی تسهیل میشود که میتواند زنجیرههای هیدروکربنی را بازآرایی و شکسته و همچنین هیدروژن را به مواد آروماتیک و الفینها برای تولید نفتنها و آلکانها اضافه کند.
محصولات عمده حاصل از هیدروکراکینگ سوخت جت و گازوئیل است، اما فراکسیون نفتای کم گوگرد و LPG نیز تولید می شود.[15] همه این محصولات دارای محتوای بسیار کم گوگرد و سایر آلاینده ها هستند.
در اروپا و آسیا بسیار رایج است زیرا این مناطق تقاضای زیادی برای گازوئیل و نفت سفید دارند. در ایالات متحده، ترک خوردگی کاتالیزوری سیال رایج تر است زیرا تقاضا برای بنزین بیشتر است.
فرآیند هیدروکراکینگ به ماهیت ماده اولیه و نرخ نسبی دو واکنش رقیب یعنی هیدروژناسیون و کراکینگ بستگی دارد. مواد اولیه معطر سنگین تحت طیف وسیعی از فشارهای بسیار بالا (1000-2000 psi) و دماهای نسبتاً بالا (750-1500 درجه فارنهایت، 400-800 درجه سانتیگراد)، در حضور هیدروژن و کاتالیزورهای خاص به محصولات سبک تر تبدیل می شوند.
بدون دیدگاه